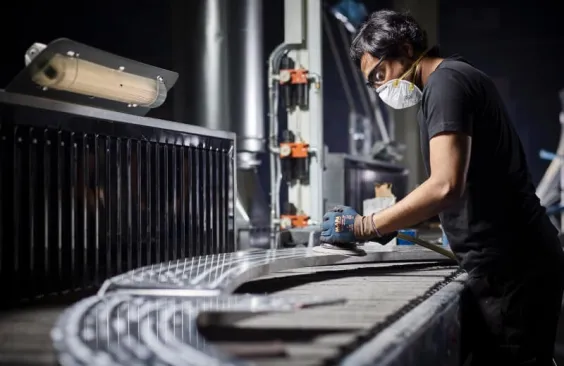
We support product development from early stage industrialization to final manufacturing and production process design. Making this possible is our next-generation machines and highly skilled team of:
- CAD/CAM designers and programmers
- Tool makers
- Application and manufacturing engineers
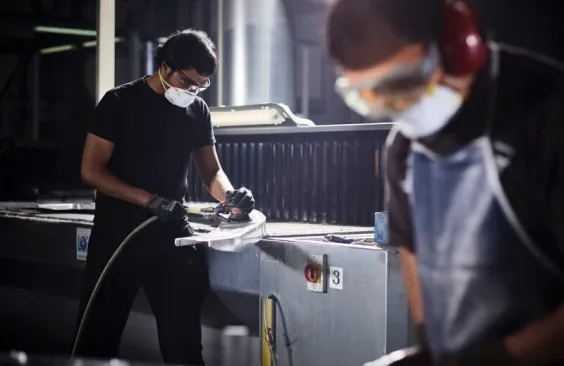
Our manufacturing engineering solutions include:
- Process capability studies
- Precision machining
- Industrialization
- CAD/CAM programming
- Application engineering
- Manufacturing process design
- Production process development
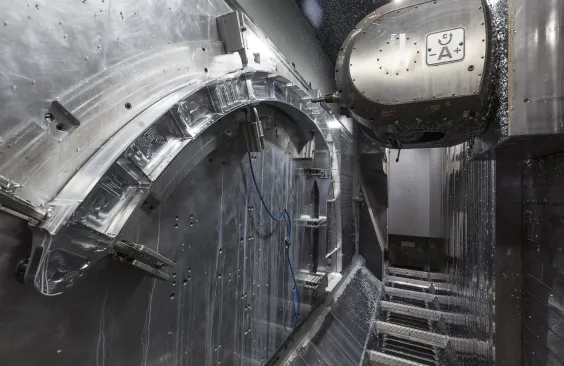
Our machining capabilities are designed to meet key industry requirements with the following offerings:
- Three-and five-axis milling machining soft and hard materials
- Turning
- EDM
- Laser , TIG , MIG and ARC welding
- Rectification process (roll forming, shot peening by ultrasonic and blasting)
EPI also offer equipping and Sub-Assemblies process :
- Assembly for faster installation
- Assembly for Torqueing
- Assembly for bushing
- Assembly for bearing installation
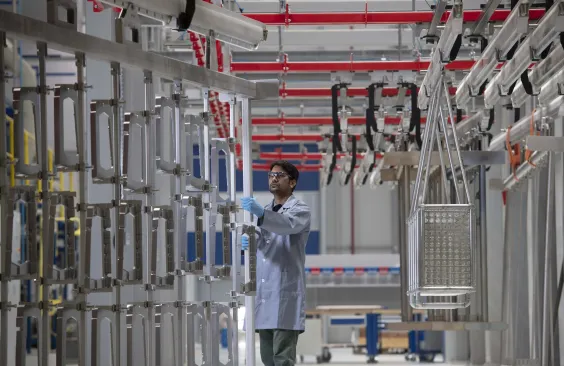
Chemical Processing
- Chemical cleaning, degreasing of Aluminum & Titanium Alloys
- Pre-penetrant Etching of Aluminum & Titanium Alloys
- Ultrasonic Cleaning Aluminum & Titanium Alloys
- Solvent Degreasing Aluminum & Titanium Alloys
- Anodizing of Aluminum
- Tartaric Sulphuric Acid Anodizing
- Boric Sulphuric Acid Anodizing
- Sulphuric Acid Anodizing
- Chromic Acid Anodizing
- Chemical Conversion Coating of Aluminum
Non Destructive Testing
- Fluorescent Penetrant Testing
Surface Enhancement
- Dry Blasting & Paint Stripping
- Shot peening for fatigue enhancement metal ( Robotic & Manual)
Paint Process
- Painting (Water & Solvent borne) with automated curing cycle and ink marking
- Sol-gel conversion coating
Part Marking
- Continuous Inkjet Marking
- Electro Chemical Etch Marking
- Marking Protection by Varnish
Laboratory
- Chemical Analysis by
- Inductively Coupled Plasma Optical Emission Spectroscopy (ICP-OES)
- Spectrophotometer
- Auto titration
- pH Measurement using glass electrodes
- Conductivity Measurement using glass electrodes
- Surface Tension using digital Tensio Meters
- Corrosion Test (ISO 9227 & ASTM B117)
- Dye-Spot Test (ISO 2143)
- Intergranular Attack & Pitting Examination
- Etch Rate Determination of Metals
- Hydrogen Embrittlement Test (ASTM E1447)
- Coating Inspections:
- Paint Adhesion Test
- Solvent Resistance Test
- Paints & Varnishes - Cross-Cut Test (ISO 2409)
- Paints & Varnishes - Determination Of Resistance To Liquids (ISO 2812-2)
- Bend Test (ISO 1519)
- Eddy current Thickness Measurement of painted parts/specimens (ISO2808)
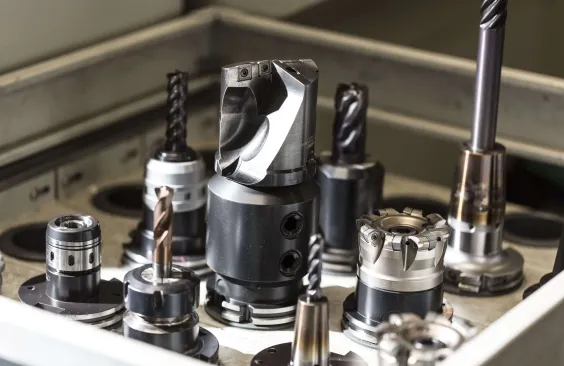
All our cutting tools and re-sharpeners come with the assurance of quality and precision. We have an advanced technology edge to produce high-quality tools for all types of operations, such as milling, drilling, reaming, etc. Further, our capabilities extend to measuring, inspection, and other critical functions such as:
- Custom-made cutting tools for all operations
- Manufacture and re-sharpening of carbide and HSS tools
- Five-axis cutter grinders to tool re-sharpening
- Self-measurement probes and 3D simulators
- Measuring and inspection of cutting tools
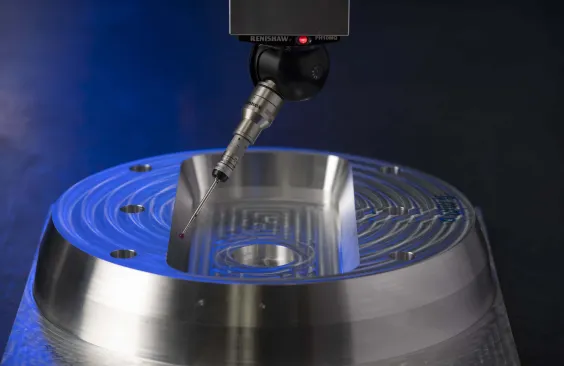
We make sure that all our products and manufacturing processes are constantly monitored and controlled to meet our internal and customer needs. That’s why we focus on training our employees for operator qualifications and reassessment programmes. This helps us promote self- inspection deployments across departments.
Our Statistical Process Control framework goes a step further by helping us improve sampling methods and redefines key characteristics required to ensure alignment with our Quality Policy.
Our inspection process is handled with conventional equipment like:
- Vernier caliper
- Micrometres
- Digital height gauge measuring equipment
- Coordinate Measuring Machines (CMM) Up to 7m in length
- Hexagon machine with PCDMIS for offline programming
CMM TYPE | BRAND | MEASURING LENTH(X:Y:Z) MM | SOFTWARE | VERSION |
---|---|---|---|---|
Fixed | Hexagon | 2000:5000:1500 | PCDMIS CAD++ | 2012 |
Fixed | Hexagon | 900:2000:800 | PCDMIS CAD++ | 2013 |
Fixed | Hexagon | 700:700:500 | PCDMIS CAD++ | 2013 |
Portable | Hexagon | 1 Meter Radial | PCDMIS CAD++ | 2011 |
OFF-line Programming dongle | Hexagon | N/A | PCDMIS CAD++ | 2012 |
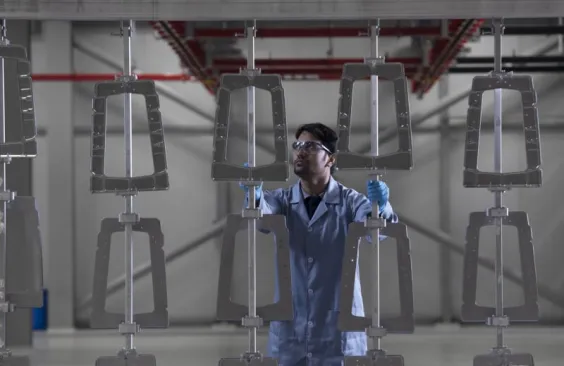
We are equipped to control the properties of materials, including various aluminium grades, titanium, steel and stainless steel, to meet industry benchmarks. We achieve this through monitoring that includes incoming inspections, detailed inspection during the parts manufacturing stage, and review following heat-treatment processes.
Our test capabilities include:
- Material surface hardness with machines capable of achieving Vickers, Knop, and Rockwell A, B, C methods
- Microstructure analysis (including moulding)
- Chemical analysis with spark optical emission spectrometer (OES)
- Electrical conductivity measuring of non-ferrous material (aluminium grade/Eddy currents)
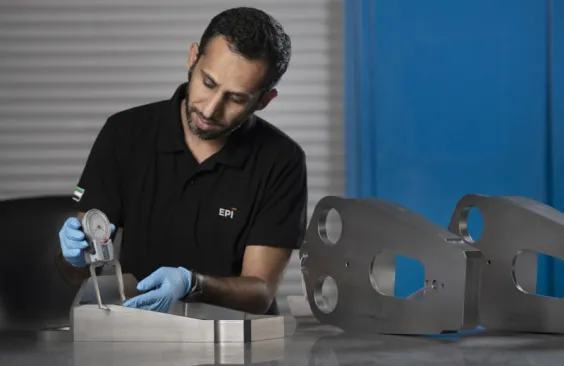
Dimensional, force, torque, electrical, furnace We perform in-house calibration for equipment within our scope of processes (excluding master equipment). This may include covering dimension force, torque, electrical, and furnace.
Our calibration offering is handled by our dedicated software platform that tracks all related data and notifications. This allows recall of equipment as per the defined verification period, supported by a qualified team.
